Tyre
Tyres are manufactured according to relatively standardised processes and machinery available worldwide in around 455 tyre factories. With over 1 billion tyres manufactured worldwide annually, the tyre industry is a significant consumer of natural rubber. Tyre factories start with bulk raw materials such as synthetic rubber, carbon black, and chemicals and produce numerous specialised components assembled and cured.
The tyre is an assembly of numerous components built upon a drum and then cured in a press under heat and pressure. Heat facilitates a polymerisation reaction that crosslinks rubber monomers to create long elastic molecules.
In India, there are many tyre manufacturing plants of different companies, including Yokohama Rubber Company, Apollo Tyre, Ceat Tyres, J.K. Tyres, MRF and TVS Tyres and many others.
Many different parts go into the making of a tyre as follows.
- Beads
- Belt
- Ply
- Sidewall
- Sipe and Groove
- Shoulder
- Tread
Preparation
Raw materials for the preparation of the Tyre are Rubber – Natural + Synthetic, Polythene, Carbon Black, Silica, Sulphur, Zinc Oxide, Stearic Acid, Accelerators and Retarder – Catalysts & Fabric.
The Banbury mixer is a sophisticated piece of heavy equipment with a mixing chamber with two rotors inside. The rotor is named BANBURY ROTOR, and the chamber is BANBURY CHAMBER. There are two rotors; both the rotors rotate in opposite directions at a certain speed. The mixing occurs between the rotor tip and the chamber and not between the two rotors. Needling takes place between the two rotors. Each element added in mixing has its importance, i.e. Sulphur acts as a curing agent, Zinc Oxide and Steric Acid increase the speed of the curing time, and accelerators and retarders provide dispersive mixing. The batch is injected at a temperature of 135°C, and batch damping occurs at 165°C.
Applications
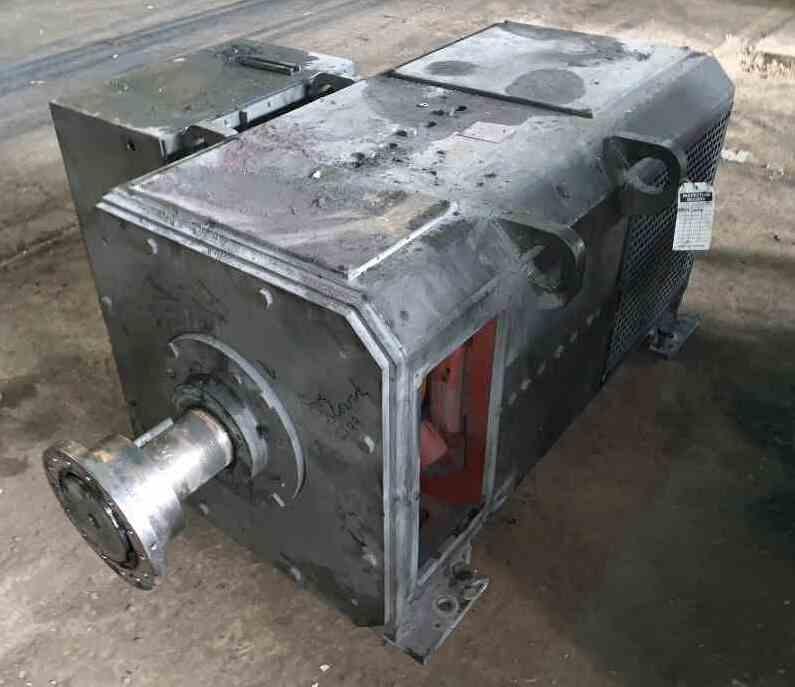
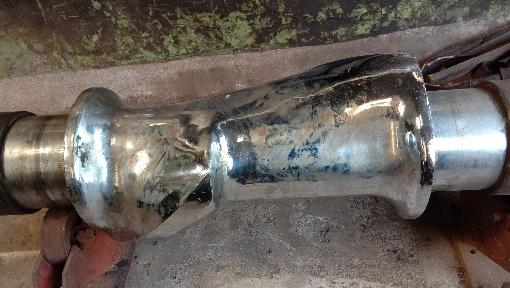
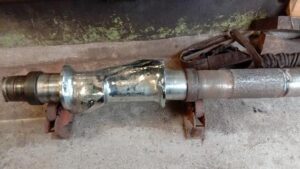
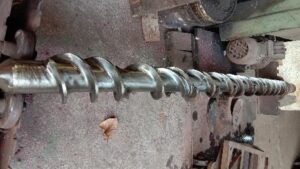
Solutions
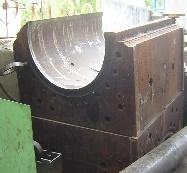
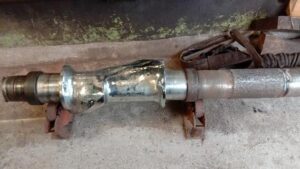
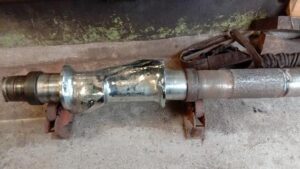
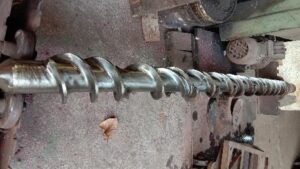
Experience of EWAC
- We have experience in the reclamation of Banbury Rotor, Chamber and Extruder screw.
- We take this job, as a turnkey project and deliver the reclaimed component saving time and costing.